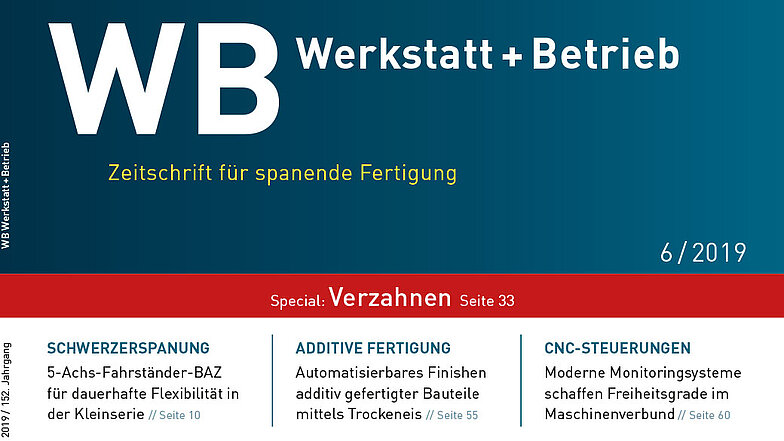
JPG
Bild für redaktionelle Zwecke
Die digitale Ära setzt zwei wesentliche Trends in Gang: Zum einen entstehen immer größere Betriebe, die durch Skaleneffekte bei geringer Produktvielfalt wirtschaftlich produzieren. Zum anderen differenzieren sich kleinere und flexiblere Werkstätten aus, die ihre Produktionsanlagen teils sogar für jeden Kunden individuell anpassen (Abbildung 1). In diesem Kontinuum möglicher Wertschöpfungskonstellationen entstehen für die Betriebe vielfältige Optionen, sich mithilfe digitalisierter Prozesse schneller an die sich wandelnden Anforderungen der Kunden anzupassen. Gleichzeitig wächst aber auch der Kostendruck aufgrund des globalisierten und kompetitiven Marktes. Wer frühzeitig in Automatisierung investiert, kann seine Fertigung zukunftssicher aufstellen und Effizienzgewinne schnell in Wettbewerbsvorteile umsetzen.
Größte Herausforderung, um den Betrieb weiter zu automatisieren, ist es, den Sägeprozess von Maschine und Werkzeug bis zur Warenwirtschaft zu verketten. Denn diese Aspekte sind noch immer neu für die Branche: Einer Umfrage des Fraunhofer Instituts für Produktionstechnik und Automatisierung IPA unter 66 Unternehmen aus dem Metallhandel zeigte, dass 79 Prozent keine Erfahrung mit Industrie-4.0-Anwendungen haben.* Und auch von den heute im deutschen Markt existierenden Sägemaschinen verfügen nur rund 30 Prozent über eine moderne, digitale Steuerung, weltweit sind es nur etwa zehn Prozent. Darum erfassen die Betriebe ihre Daten bisher größtenteils schriftlich oder lokal in der Maschinensteuerung, wodurch diese oft nicht in die digitalen Informationssysteme eingebunden werden können. Zudem fehlt es der Branche an standardisierten Schnittstellen, um den Datenaustausch über die gesamte Prozesskette hinweg zu ermöglichen. Dadurch können andere Maschinen, Peripherie und Software nicht auf Maschinendaten zugreifen, der Zustand des Prozesses sowie der Maschine sind nicht transparent. Dabei ist Transparenz laut Studie des Fraunhofer IPA einer der wichtigsten Aspekte von Industrie 4.0 (Abbildung 2). Doch die heterogenen Maschinenlandschaften sind von vielen verschiedenen Protokollen und etlichen Steuerungen geprägt, was die Kommunikation erschwert. Je höher der Standardisierungsgrad einer Schnittstelle, desto geringer der Integrationsaufwand.
Bereits auf dem Markt verfügbar sind verschiedene Industrie-4.0-Lösungen für Assistenzsysteme, Condition Monitoring und Predictive-Maintenance-Anwendungen, aber auch Konzepte für die Werkzeugverwaltung. Letztere kommen beispielsweise von den Unternehmen iBlade und c-Com: Angefangen bei der Stückzahl einzelner Werkzeuge und ihrer Ortung im Unternehmen bis hin zu Werkzeuginformationen mit Nachschleifmanagement können diese alle relevanten Informationen abrufen, verwalten und sogar mit dem Bestellwesen verknüpfen. Im Ergebnis wird die Wertschöpfungskette transparenter, der Beschaffungsaufwand sinkt und redundante Strukturen in der Werkzeughistorie lassen sich vermeiden.
Darüber hinaus bietet der Markt auch Tools für die Unterstützung des Maschinenbedieners und des Prozesses im Voraus, um die Maschinen-, Werkzeugparameter und das Programm einzustellen. So unterstützt bei-spielsweise das online und als Smartphone-App verfügbare Programm ParaMaster® von dem Unternehmen WIKUS-Sägenfabrik dabei, Sägebänder auszuwählen und Schnittparameter sowie Schnittkosten zu ermitteln und so Maschine und Band optimal aufeinander abzustimmen. Folgt der User den Empfehlungen des Tools, kann er seine Kosten pro Schnitt signifikant senken. Mit rund 4.500 Bandsägemaschinendaten von 102 Herstellern sowie etwa 60.000 Werkstoffbezeichnungen bildet das Tool eine Vielzahl von Anwendungsfällen ab. Die Datenbasis wächst täglich und wird in enger Zusammenarbeit mit Maschinenherstellern stetig aktualisiert. Anwender erhalten so schnell und einfach eine konkrete Empfehlung von Sägebändern einschließlich der empfohlenen Schnittparameter. Darüber hinaus können Nutzer weitere Randbedingungen wie Stundensätze für die Produktionskosten und Standzeiten der Sägebänder eingeben und erhalten dadurch sehr realitätsnahe Schnittkosten. In Verbindung mit einem auf dem Band aufgebrachten QR-Code erhöht dies weiter den Automatisierungsgrad der Sägebandauswahl: Wird der Code über die ParaMaster®-App eingescannt, werden die Daten des Bandes automatisiert übertragen, wodurch sich Eingabefehler vermeiden lassen. Der Anwender muss nur noch seine Maschine und den zu sägenden Werkstoff auswählen und erhält die passenden Schnittparameter. Zudem plant WIKUS aus ParaMaster®- heraus mit einem Klick Angebote zu generieren, die zu Maschine und Anwendung passen, um dem Anwender einen weiteren zeit- und kostenintensiven Schritt zu ersparen
Obwohl bereits einschlägige Erfolgsgeschichten sichtbar sind, befinden sich insbesondere kleine und mit-telständische Unternehmen noch in einer frühen Phase, in der noch viel Raum für eine Digitalisierung der Geschäftsprozesse vorhanden ist. Zwar sind die Möglichkeiten noch begrenzt, um die Fertigung mit den am Markt existierenden Produkten vollständig zu vernetzen. Doch erlauben die vorhandenen Initiativen bereits erste Tests mit digitalen Lösungen, um die Vorteile von Industrie 4.0 auch für Anwendungen in der Säge-technik zu verdeutlichen. Künftig werden zudem auch Plattform- und Ecosysteme entstehen, bei denen Maschinen- und Sägebandhersteller mit Softwareanbietern kooperieren, um eine weitergehende Automati-sierung zu ermöglichen. Auch WIKUS plant bereits weitere Programme, um seine Produkte und Services noch digitaler aufzustellen.
Diana Thiel, Marketing