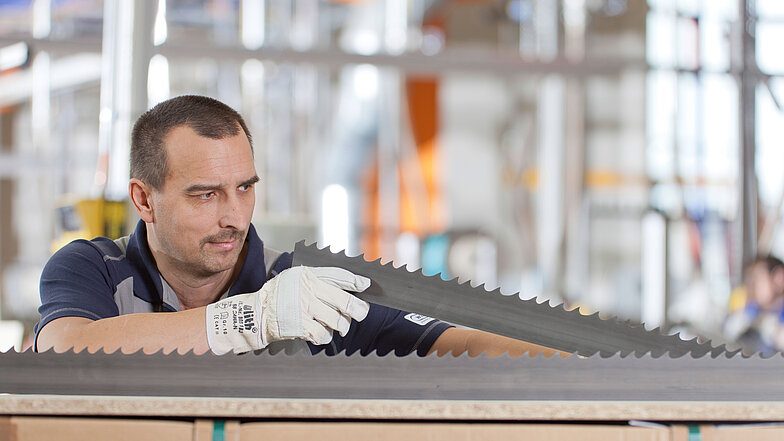
JPG
Image for editorial purposes
If a band saw blade experiences sudden failure, it is usually due to improper interaction between man, machine, cutting material and band saw blade. Although technical problems such as wear factors or premature tool failure may occur in any sawing operation, they are often preventable. It is important that operators are familiar with the possible reasons for failure and their causes in order to have effective countermeasures at their disposal.
Wear and tear, i.e. wear of the cutting teeth resulting from use, is a natural part of the life span of sband saw blades, which are subject to high physical loads on a daily basis. Nevertheless, a distinction must be made between normal wear and severe premature wear. There are many factors responsible for unnaturally fast wear of cutting teeth. Here, temperature at the tooth cutting edge during the machining process is critical. This can be influenced by the choice of suitable cutting parameters and material (material number or DIN designation, material strength and microstructure, material dimensions and the nature of the material surface.)
WIKUS, for example, has developed the ParaMaster®, including a smartphone app, for selecting the ideal cutting parameters such as cutting speed, cutting performance and feed rate: a tool that makes it easy for operators to perform difficult configuration work. The online cutting data programme with up-to-date data from 150,000 materials and 4,500 band saw machines helps to optimise sawing processes, as it recommends suitable cutting parameters to the user from to its extensive application know-how. A sufficient supply of a coolant, which is suitable for the materials being cut, is also necessarily. This is also recommended by ParaMaster.
In addition, sanded, truncated or extremely hard material surfaces, or very high material strengths, can cause service life issues if adjusted incorrectly. Because material hardness is directly correlated with higher cutting temperatures, this can lead to premature wear. Incorrect first also poses a big problem. Excessive stress during improper insertion causes micro-breakages at the cutting edge. These can reduce the possible service life by up to 40% and therefore lead to premature end of life. Last but not least, the chip brush also plays an important role in reducing wear. It gently removes chips from the saw band and clears the chip space. If the chip brush is not renewed in time or if it is not correctly adjusted, this will have a negative effect on the service life.
Tooth breakage is not a natural cause of end of life. Usually, tooth breakage only occurs when the teeth are overloaded. The causes are: an excessively low cutting speed in relation to a high feed rate or poor choice of tooth pitch, e.g. unsuitable for the material cross-section . It is imperative to secure the cutting material as effectively as possible. Any movement of the material during sawing may lead to tooth breakage. The risk of workpiece movement increases particularly with layer or bundle cuts. For very soft materials, which tend to form built-up edges, it is crucial to ensure a high oil content in the cooling lubricant as well as a functional chip brush. In rare cases, harder components in the cutting material can also lead to tooth breakage.
Premature cutting deviations are also unnatural. The causes could be: The band guide is not keeping the band precisely in the cutting direction and the guides are at an angle. Another issue could be that the lateral band guide on manual machines with non-hydraulically biased guides is not tight enough. Also if the distance of the band guides to the workpiece is too great, the feed rate excessive or band tension too low, this may lead to premature cutting deviations. A cutting deviation after short-term use may be caused by asymmetrical mechanical damage of the cutting teeth, e.g. by harder components in the cutting material. Another cause may be damage to the band by the chip brush, e.g. over-tightened steel wire brush or use of abrasive plastic polishing brushes. However, with normal saw band use and therefore with even wearing, cutting deviations of the cutting teeth are a natural end of life condition.
The failure of a band saw blade by band breakage is usually due to mechanical damage of the carrier band during the cutting process. It is important to identify the exact source of the problem in order to prevent another band break. The most common cause of band breakage lies in the area around the band guides. Lateral band guides may be poorly adjustment or worn, rear band guides may be worn. When worn, these can damage the band edges or the rear band edge, this results in a structural transformation to frictional martensite, which causes micro-racking with resulting band breakage.
Other causes could be excessive band tension, faulty rotor bearings, poor alignment between rotor and rear belt guides, excessive starting of the belt rear on the rotor flange or rotor failure - i.e. concentricity deviations, rotor conicity.
A seam weld break constitutes an unnatural premature failure of the saw band. This is caused by an error in the manufacturing process of the weld. If no consequential damage can be detected and the toothed cutting edges are subject to normal wear, the band may be repaired for further use through re-welding. For this reason, the procedure in case of welding seam breakage is basically: return the broken saw band and do not dispose of it immediately. Manufacturers like WIKUS check repairability, perform the repair and return the band afterwards.
In the future, sawmills will become more and more digital and therefore more fail-safe: With predictive maintenance, the necessary wear-related repairs are systematically supported, therefore avoiding unplanned downtime. Today, many machines already incorporate sensor technology, e.g.: coolant monitoring, cutting control, cutting force monitoring, etc. This also helps to detect weak points early on and avoid unplanned downtime or unwanted rejects. If the same problems occur frequently, this is an indicator of a weaknesses in the machine.
Unforeseen band failures are a significant cost factor, but by paying attention to the above aspects and switching to digitised and predictive troubleshooting, you can delay or prevent many instances of failure.
Further education and training also help to ensure greater safety when dealing with saw bands. For this purpose, WIKUS founded the WIkademy®, a training center based in Spangenberg, Hesse. On-site seminars range from the basics to expert knowledge about sawing technology, the right applications and analysis and elimination of the causes of failure. You can learn more about the causes of failure and their elimination there, as well as in the online guide at www.wikus.de.
Elke Sachs, Head of Marketing