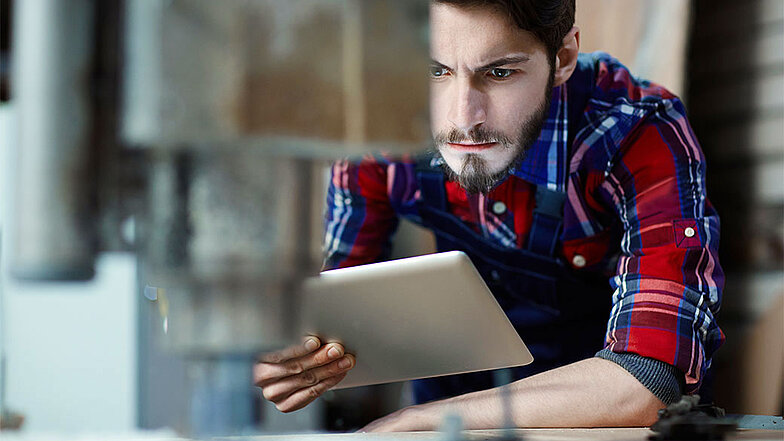
JPG
Image for editorial purposes
Sawmills usually have two different objectives: To reduce costs and/or increase productivity. Which aspect has priority in your opinion?
Stefan Schwenda: Most companies generally want to do both, reduce costs and increase productivity. The total costs, i.e. machine costs, labour costs and tool costs should always be taken into account. After all, the allegedly expensive band saw blade does not always cause higher costs. The opposite is true: If you need to produce many saw cuts in a very short time, it is worth investing in new technologies, but above all in a high-quality and efficient band saw blade that combines high cutting speeds with high cutting performances and standing surfaces. Thus, about six to seven times as many cuts are possible in the same time. This time saving reduces the machine and personnel costs and thereby also the total costs. Depending on the applica-tion, it saves around 30% of the costs compared to a cheap band saw blade. Then there is also the additional machine capacity as the jobs are completed faster.
In addition, there are companies that change to a cheaper bimetal band saw blade in the evening, which reduce the cutting parameters and saw unmanned at night. Although this saves personnel costs, the reduc-tion of the parameters increases the machine costs. This is also rather disadvantageous for the band saw blade and shortens the blade-life. However, those who apply the most effective parameters don’t need the unmanned night shift because the saw cuts have already been processed.
How popular are the digital solutions that are already available on the market from your perspective?
Stefan Schwenda: We see a huge acceptance of digital solutions in the market. The focus is always on: What is the concrete benefit for the skilled worker?
A concrete added value was also the basic concept of our blade selector and our online editing data program ParaMaster. The latter is also available as an app. This allows both the planner and the machine operator to determine which band saw blade is the right one for their application and they can display cutting data directly for their specific application.
Digitisation also means transferring these values into the machine, or even getting values out of the machine. In many cases, however, the prerequisites – especially for older models – have not been achieved, because in most cases the systems do not yet have the appropriate software and hardware.
How must the market change so that digitisation and automation can continue?
Stefan Schwenda: Collecting and analysing relevant data is one of the most important factors for companies in digitisation. By analysing data, it is possible to gain important insights for operational management as well as the development of new products and services. Companies must therefore capture and analyse the information generated by networked machines, tools, workpieces and employees. This makes the processes in the production halls more transparent and can be automated further. However, this only works if each component and workpiece has information about itself and can communicate with other objects in the surrounding area.
We work closely with machine manufacturers on new technologies. And not only for better networking between the machine and blade. Older machines can be equipped with sensors; the solutions already exist. In the future, the goal should be an intelligent symbiosis of machine and tool.
What concrete steps should market participants now take?
Stefan Schwenda: At WIKUS, we are actively approaching the machine manufacturers in order to promote new technologies and concepts for networking. But often the machine manufacturers do not want to tie themselves to one supplier of saw blades. So they face the challenge of working with several companies like us to develop solutions, and that takes time. There is a huge need to catch up, especially in the steel and metal trade. For example, there are no uniform part numbers for the same products from different manufacturers. The reason for this is often a conservative silo mentality and the concern about increasing competition. But it exists right now.
I therefore see a great opportunity in common industry standards – from article numbers of steel products to software interfaces. Only then can the user ultimately network different machines and tools in his production and profit from efficiency gains. In general, we can say that the digitisation of sawing processes offers po-tential savings of between 25 and 45 percent because it reduces machine-related process costs as well as machine and organisation-related downtimes.
Elke Sachs, Head of Marketing