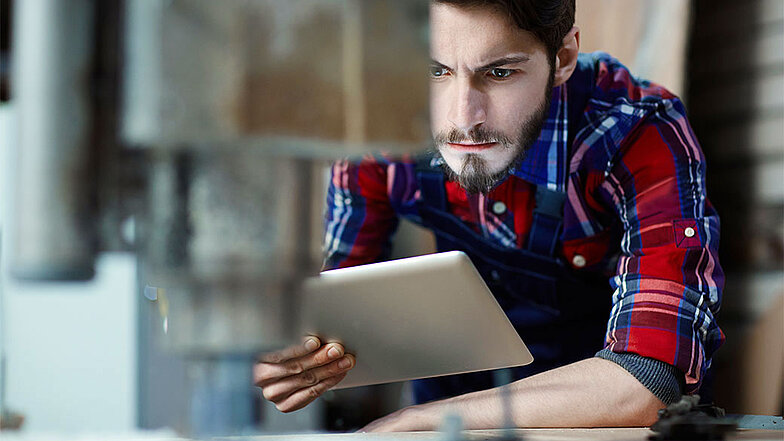
JPG
Bild aus dieser News für redaktionelle Zwecke
Sägebetriebe haben in der Regel zwei verschiedene Zielstellungen: Kosten senken und/oder Produktivität erhöhen. Welcher Aspekt hat Ihrer Meinung nach Priorität?
Stefan Schwenda: Die meisten Unternehmen wollen in der Regel beides, Kosten senken und die Produktivität erhöhen. Dabei sollten immer die Gesamtkosten, also Maschinenkosten, Personalkosten und Werkzeugkosten in Betracht gezogen werden. Denn nicht immer verursacht das vermeintlich teure Sägeband auch höhere Kosten. Ganz im Gegenteil: Sind etwa in kürzester Zeit viele Sägeschnitte abzuarbeiten, lohnt sich die Investition in neue Technologien, aber vor allem auch in ein hochwertiges und leistungsfähigeres Sägeband, das hohe Schnittgeschwindigkeiten mit hohen Schnittleistungen und Standflächen kombiniert. Somit sind in derselben Zeit ca. sechs- bis siebenmal so viel Schnitte möglich. Diese Zeiteinsparung reduziert die Maschinen- und Personalkosten und dadurch auch die Gesamtkosten. Man spart je nach Anwendung rund 30 % der Kosten gegenüber einem günstigen Sägeband. Dazu kommt die zusätzliche Maschinenkapazität, da die Aufträge schneller fertig sind.
Darüber hinaus gibt es Betriebe, die am Abend auf ein günstigeres Bimetallsägeband wechseln, die Schnittparameter reduzieren und in der Nacht mannlos sägen. Dadurch werden zwar Personalkosten gespart, aber durch die Reduzierung der Parameter erhöhen sich die Maschinenkosten. Auch ist dies eher nachteilig für das Sägeband und verkürzt die Standzeit. Wer aber die effektivsten Parameter anwendet, spart die mannlose Nachtschicht, weil die Sägeschnitte schon abgearbeitet wurden.
Wie gefragt sind aus Ihrer Perspektive die heute schon verfügbaren digitalen Lösungen am Markt?
Stefan Schwenda: Wir sehen eine große Akzeptanz von digitalen Lösungen am Markt. Dabei steht immer im Fokus: Was ist der konkrete Nutzen für den Facharbeiter?
Ein konkreter Mehrwert war auch der Grundgedanke unseres Bandselektors und unseres Online-Schnittdatenprogramm ParaMaster, letzteres ist auch als App verfügbar. Damit können sowohl die Planer als auch die Maschinenbediener ermitteln, welches Sägeband sie für ihren Anwendungsfall das Richtige ist und können Schnittdaten direkt für ihren konkreten Anwendungsfall anzeigen lassen.
Digitalisierung bedeutet auch, diese Werte in die Maschine zu übertragen, bzw. auch Werte aus der Maschine zu bekommen. In vielen Fällen sind aber die Voraussetzungen – gerade bei älteren Modellen – noch gar nicht geschaffen, weil die Anlagen in den meisten Fällen noch nicht über die entsprechende Software und auch Hardware verfügen.
Wie muss sich der Markt verändern, damit die Digitalisierung und Automatisierung weiter voranschreiten kann?
Stefan Schwenda: Das Sammeln und Auswerten relevanter Daten ist einer der wichtigsten Faktoren für Unternehmen bei der Digitalisierung. Durch die Analyse von Daten lassen sich wichtige Erkenntnisse für die operative Steuerung sowie die Entwicklung neuer Produkte und Leistungen gewinnen. Unternehmen müssen daher die Informationen, welche durch vernetzte Maschinen, Werkzeuge, Werkstücke und Mitarbeiter entstehen, erfassen und analysieren. Dadurch werden die Abläufe in den Produktionshallen transparenter und lassen sich weitergehen automatisieren. Das funktioniert jedoch nur, wenn jedes Bauteil und Werkstück Informationen zu sich selbst besitzt und mit anderen Objekten in der Umgebung kommunizieren kann.
Wir arbeiten mit Maschinenherstellern eng an neuen Technologien zusammen. Und das nicht nur für eine bessere Vernetzung von Maschine und Band. Ältere Maschinen lassen sich mit Sensoren ausstatten, Lösungen dafür gibt es schon. Zukünftig sollte das Ziel eine mitdenkende Symbiose aus Maschine und Werkzeug sein.
Welche Schritte sollten die Marktteilnehmer jetzt konkret gehen?
Stefan Schwenda: Wir bei WIKUS gehen aktiv auf die Maschinenhersteller zu, um neue Technologien und Konzepte für die Vernetzung voranzutreiben. Doch oft wollen sich die Maschinenhersteller nicht an einen Anbieter von Sägebändern binden. Sie stehen also vor der Herausforderung, mit mehreren Unternehmen wie uns Lösungen zu erarbeiten und das nimmt Zeit in Anspruch. Insbesondere im Stahl- und Metallhandel besteht großer Aufholbedarf. Hier gibt es beispielsweise keine einheitlichen Artikelnummern für dieselben Produkte unterschiedlicher Hersteller. Grund ist hierfür häufig ein konservatives Silodenken und die Sorge über zunehmenden Wettbewerb. Doch der existiert bereits heute schon.
Eine große Chance sehe ich daher in gemeinsamen Branchenstandards – über Artikelnummern von Stahl-produkten bis hin zu Softwareschnittstellen. Denn nur so kann der Anwender letztlich verschiedene Maschi-nen und Werkzeuge in seiner Fertigung miteinander vernetzen und von Effizienzgewinnen profitieren. Im Allgemeinen kann man sagen, dass in der Digitalisierung der Sägeprozesse ein Einsparpotenzial von 25 bis 45 Prozent steckt, weil sich maschinenbedingte Prozesskosten sowie maschinen- und organisationsbedingte Stillstände damit reduzieren lassen.
Bild aus dieser News für redaktionelle Zwecke
News als PDF Version
Elke Sachs, Leitung Marketing