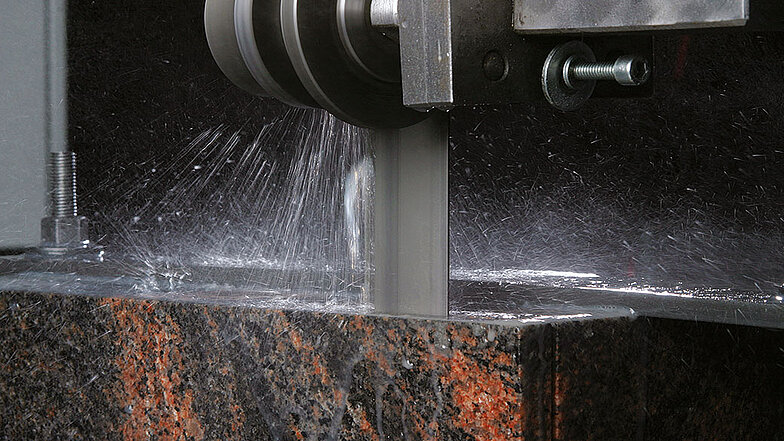
JPG
Image for editorial purposes
As the hardest material, diamond is capable of machining almost all materials where other cutting materials fail due to their physical and technological properties. Diamond-coated band saw blades are therefore the first choice for cutting very hard abrasive and mineral materials, natural stones and technical glasses.
The choice of cutting material - carbide, bimetal or diamond - depends on the materials being cut and their machinability. Diamond is known to be the hardest material and can therefore cut almost all materials - even the hardest. Of course this does not mean that diamond saw bands are fundamentally superior to other band saw blades: For example, in construction, case-hardened, tempering and tool steels carbide or bimetallic bands are usually used, which are quite sufficient for most materials.
Diamond, on the other hand, is used for special applications and for cutting glass, graphite, silicon, hard coal, ceramics, concrete materials, CFRP, sintered materials, perforated bricks and clinker as well as to cut mineral building materials such as calcareous or natural stone. This is why diamond-coated band saw blades are primarily used in transportation such as aerospace, energy and recycling as well as construction and steel making.
Diamond-coated band saw blades offer the highest level of precision at high cutting speeds and performance. This special band saw blades can even be used when machining graphite, where cooling is generally not possible and therefore is performed dry. That’s why companies use diamond-coated band saw blades to make electrode blanks from graphite. Technically speaking, it is basically correct to describe the use of diamond-coated band saw blades as a cut-off grinding process. In contrast to graphite, water cooling is used during the sawing of optical glass and/or silicon. For comparably expensive materials, precise and materialsaving cutting is also crucial in order to ensure cost-effectiveness. Only diamond-coated band saw blades in this form can guarantee this. In addition, diamond band saw blades offer the advantage, under certain use conditions and constraints, that no chipping occurs at the contour edges during sawing and that hardly any reworking is necessary due to their excellent cutting surface.
Diamond-coated band saw blades with stainless steel carrier band can be used particularly efficiently when cooling with oil-free or corrosion-free coolants or even pure water, because the carrier band is not damaged from potential oxidation and decomposition during prolonged periods of downtime. Accordingly, the bands need to be changed less. In case of sporadic use, the saw bands can remain clamped on the sawing machine.
The pad geometry and grain size of diamond band saw blades differ according to the range of potential applications. While a continuous diamond coating is suitable for small material dimensions, band saw blades with segmented diamond coverage are selected for medium-sized workpieces. Interrupted diamond coverage is usually used for large workpiece dimensions. Due to the existing large chip space, which ensures removal of the resulting waste material, high cutting performance and cutting times are possible.
Comprehensive advice, as offered by WIKUS, is crucial when selecting the right band saw blade. Because, depending on the material or the workpiece being machined, custom design of the occupation geometry is both expedient and possible. Furthermore, diamond-coated band saw blades have a wide range of applications, which is why both the use and, above all, the handling of diamond band saw blades require extensive know-how from skilled workers. That's why sawmills should be advised in advance by experts. Further education and training also help to increase safety when dealing with diamond-tipped band saw blades and to benefit fully from the advantages also in terms of efficiency. For this purpose, WIKUS founded the WIkademy®, a training center based in Spangenberg, Hesse. The program offers on-site seminars with a methodological mix of lessons and in-depth expertise.
Elke Sachs, Head of Marketing