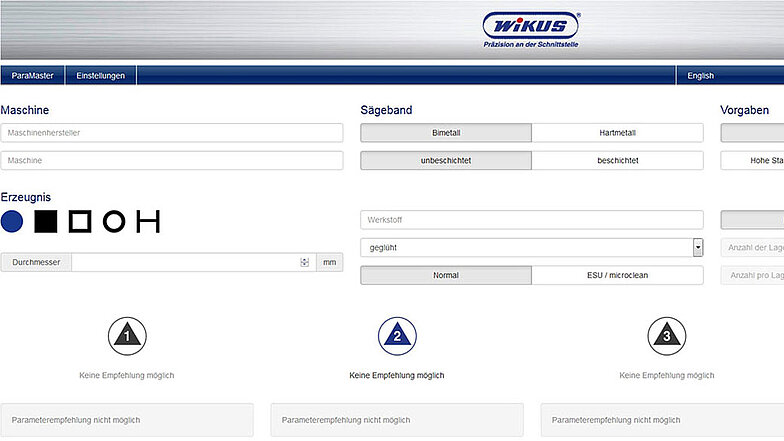
JPG
Image for editorial purposes
20 September 2018 – The resource time is an enormously important factor in the company and plays an important role especially for production processes. There is potential for improving productivity when the correct tool is selected and used efficiently in metal cutting. In addition to the selection of the optimum band saw blade, correct configu-ration of the cutting parameters can significantly boost the cost efficiency of the sawing processes by en-hancing the cutting performance and increasing the blade-life.
Support Instruments to Determine the Machine Parameters
For more than three decades, the WIKUS-Sägenfabrik has sup-plied supporting instruments for defining cutting parameters for band saw blades. For instance, the user can utilize the WIKUS cutting data slide to identify a relevant recommendation quickly and easily. By selecting the relevant material group and depend-ing on the material diameter, it can be used to recommend a cut-ting and feed speed for the bimetal and carbide product groups and also the expected cutting rate, thereby allowing the costs per cut to be optimized. In situations where there is no access to the Internet or little time for evaluation, the cutting data slide is still a helpful tool.
Digital Development with the Online Cutting Data Program ParaMaster® 4.0
In line with the trend toward digitization, WIKUS caused a revolution in 2006 with its first version of the online program ParaMas-ter® that was designed to identify the cutting data. The tool uses the idea behind the cut-ting data slide system and, at the same time, enhances it with influencing variables such as machine data, band saw blade types and tooth pitches.
In particular, ParaMaster® supports with the choice of band saw blade and identifying the cutting parame-ters, whilst also determining the cutting costs at the same time. If the user accepts the recommendation of the ParaMaster® results, he can significantly reduce the costs per cut.
Depth Database for High Coverage of Applications
ParaMaster® is now used in more than 80 countries across the world. It can cover almost any kind of applica-tion thanks to its 4,000 machine data from 102 manufac-turers and 40,000 material designations. On account of the complexity of the combination options when saws are used, the database now contains more than 200,000,000 data records. The database is updated almost on a daily basis in close cooperation with machine manufacturers who also profit from the use of ParaMaster®.
“Due to the fact that we have more than 6,000 active users, machine manufacturers now approach us at WIKUS to send us the latest machine data,” says Dirk Heimel, Product Developer at the WIKUS-Sägenfabrik and Developer of ParaMaster®.
After registration into ParaMaster®, the user can select their application and machine. The handling and user interface are intuitive and the software can be used without any in-depth IT know-how. In this way, the user receives fast, simple and free specific values and also several other recommendations from WIKUS band saw blades including the recommended cutting parameters for the customer-specific application. Also, the user can enter other underlying conditions, for instance production cost hourly rates and the blade-life of the band saw blades, and will receive very realistic cutting costs.
Since not every machine in production provides access to a PC, WIKUS launched the ParaMaster® app in 2017 to support users directly on site. This contains all important information the machine operator requires during the sawing process to make the optimal settings, tailored to his machine and his band saw blade, for attaining cost savings. The app is continuously opti-mized to meet the customers’ needs at all times.
Making the app available for smartphones also gives the WIKUS application engineers a digital instrument for conducting analyses together with the cus-tomer to detect improvement potential.
Further Development by Using the Opportunities of Industry 4.0
In light of the ongoing digitization and the trends connected to the term Industry 4.0, the developers at WIKUS-Sägenfabrik see plenty of opportunities to connect other systems to the ParaMaster®. For instance, today the company equips the majority of its bimetal product range with a QR code that is printed on the blade.
When scanning the QR code with the ParaMaster® app, the blade data are automatically transferred very quickly thereby avoiding the risk of input errors. The user only needs to select his machine and the material that is to be cut, and receives the optimum cutting parameters.
We are also working on an option that will allow a ma-chine and application-specific tender to be generated directly from the app thereby saving the user time and expense. Also, ParaMaster® will soon be available in more than twenty-five language versions, allowing customers from across the world the opportunity to profit from the tool and optimize their productivity.
ParaMaster® as an Effective Instrument In Practice
Van Hoorn Machining BV is a specialist for sawing technology and represents the WIKUS- Sägenfabrik in The Netherlands and Belgium. Employees of this trading company have has very positive experiences when using ParaMaster® to advise the band saw blade end users on a daily basis. Wil Verrijt, Commercial-Technical Consultant at Van Hoorn Machining BV says: “ParaMaster® represents absolute added value for our customers and us, because, often, the user does not have the necessary in-depth expertise in sawing technology. In this case, ParaMaster® allows me to give our customers the advice they need quickly and easily so they can improve the sawing process and also reduce costs. And of course, we also encourage our customers to use ParaMaster® themselves.”
The company Helmut SCHRECK GmbH & Co. KG in Halstenbek, a contract manufacturer based close to Hamburg, has relied on the ParaMaster® services for many years. The company uses the WIKUS carbide band saw blade FUTURA®, di-mensions 6,830 x 41 x 1.3 mm in 2-3 tpi to ma-chine the entire range of materials from alumi-num, structural steel, free-cutting steels through to VA 1.4571 / 1.4462. ParaMaster® not only selects the matching band saw blade types from the extensive WIKUS program, but also defines the optimum cutting parameters for the band saw blade.
Hartmut Vanselow, machine operator, says about his experience with ParaMaster®: “I have been working with ParaMaster® since I got the new machine. I am really comfortable using the recommended cutting pa-rameters and achieve very high blade-lifes. We have never suffered any damage to band saw blades or had any problems when sawing due to the proposed values. The values from ParaMaster® are always ab-solutely reliable; without this program we would not be that efficient by far.”
ParaMaster® has been continuously developed up to the current version 4.0 as a browser and app-based variant. This online tool made by WIKUS has established itself as the most precise online tool for determin-ing optimum cutting parameters in the market. It takes into account most influencing variables at an ex-tremely high technical level and is continuously updated.
Information and Registration at www.paramaster.de
Image for editorial purposes
News available as PDF files
Elke Sachs, Head of Marketing