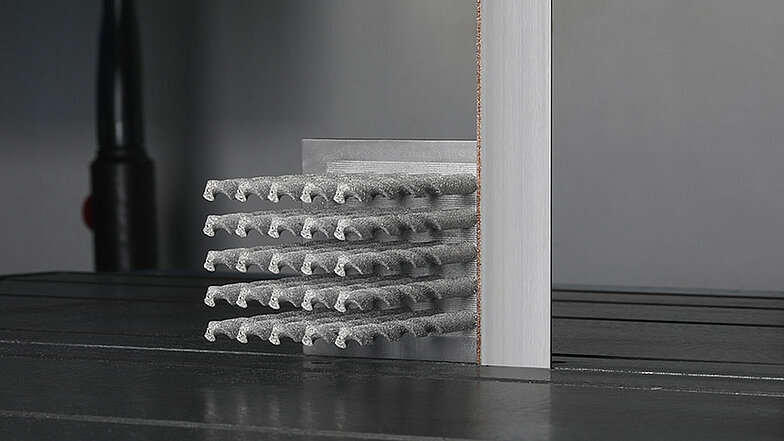
JPG
Image for editorial purposes
Hanover / Spangenberg, 17th September 2019: WIKUS-Sägenfabrik is expanding its product portfolio to include cubic boron nitride (CBN) coated CUBOGRIT® band saw blades. Cubic boron nitrite is the second hardest known material after diamond, which, in addition to its hardness and strength, also features thermal, chemical, and abrasion-resistant properties. With CUBOGRIT®, users will receive CBN-coated band saw blade technology for the first time in order to economically saw 3D hard alloys and hardened ferrous materials of up to 70 HRC. WIKUS will present the new band saw blades for the first time during the world’s leading trade fair for metalworking, the EMO Hanover.
Whilst diamond already suffers a massive loss of hardness at about 700°C, the hardness of CBN remains almost unchanged even at more than 1000°C.
For example, diamond can be ground under heat with CBN. In conjunction with the high abrasion resistance, these properties, when suitably used, ensure considerable wear resistance of the band saw blade and very good cutting surfaces. Rework is thereby significantly minimised.
The other special features lie in the carrier material made of an alloyed quenched and tempered steel, developed exclusively for WIKUS. This carrier material is optimally suited to absorbing loads and can thus be used at high cutting speeds. In addition, a higher form and dimensional accuracy can be achieved and very hard materials can be processed reliably.
Depending on the selected surface shape (K, S, U) and the grain size (B91 to B602), CUBOGRIT® is suitable for both hard alloys produced for 3D printing and the hardest alloys up to 70 HRC. The product can also be used to process hardened high speed steel (HSS), case hardened steels, high alloyed tool steels up to 55 HRC, chilled cast iron or stellite. In addition, components that have been produced in an additive manner can be separated from the plate, onto which they were previously printed, without cooling.
The fact that producing businesses are making increasing use of Additive Manufacturing in mass production is confirmed by a VDMA association survey which shows that half of its members already use 3D printing processes. “Numerous products are already being printed, above all in the automotive and aerospace industries, aerospace and medical technology. We assume that even more additive processes and products will be ready for series production in the coming years,” says Dr. Jörg H. Kullmann, Managing Partner and Business Manager Technology at WIKUS. “With the new CUBOGRIT® bandsaw blades, we are adding yet another innovation to our leading range of high-tech sawing tools and once again demonstrating that we are a major contributor to trends in the sawing industry.”
CUBOGRIT® K for small workpiece dimensions
The CUBOGRIT® K model is suitable for sawing applications with small workpiece dimensions. The band saw blade has full CBN coating at the edge of the band, allowing users to avoid chipping at the contour edges.
CUBOGRIT® S for medium workpiece dimensions
With the CUBOGRIT® S variant, specialist companies receive a segmented CBN configuration on the band edge and can individually design the configuration geometry. With its high metal cutting performance, medium-sized workpieces can be sawn economically.
CUBOGRIT® U for large workpiece dimensions
The raised segments with CBN configuration in different divisions of the CUBOGRIT® U design allow a very high metal cutting performance and consequently a short cutting time, making the product particularly suitable for large workpiece dimensions. The band saw blade has a large chip space for material abrasion and allows individual design of the segment distances.
All three versions are also available with a carrier band made of corrosion-resistant special steel as CUBOGRIT® K VA, CUBOGRIT® S VA and CUBOGRIT® U VA. For use with CUBOGRIT® , the sawing machine should allow cutting speeds of over 1200 m/min and have high machine stability and high torque of the drive motor.
Elke Sachs, Head of Marketing