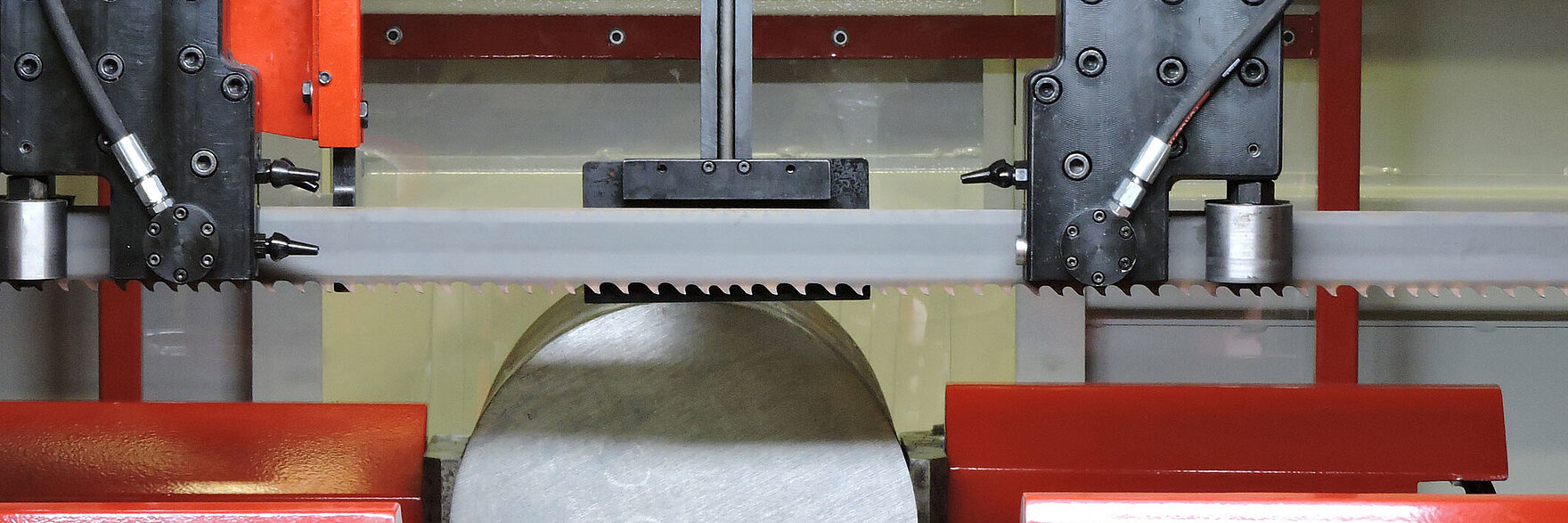
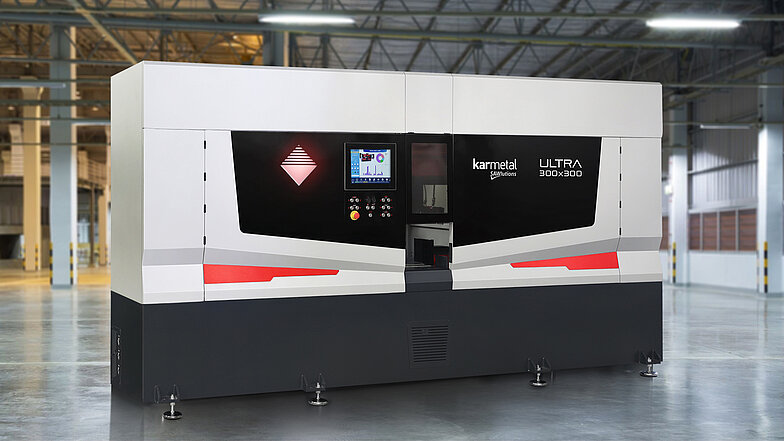
Machine partner
Since its foundation in 1975, the family-run, medium-sized manufacturer of special machines KARMETAL has been committed to producing spare parts for the automotive and defense industries. Since 1997, KARMETAL has concentrated on the production and service of band and circular saw machines.
The Turkish market leader currently sells its innovative machines in over 60 countries and supplys services from its branches in Germany and USA also.
Challenges and requirements
For the changed demands of today’s saw users, KARMETAL developed a high-performance band saw machine specifically designed for industrial applications – for example in forging plants as well as in mechanical engineering or steel trading. The manufacturer thus expanded its machine portfolio with the ULTRA 300×300 high-performance band saw machine.
This new model was designed to improve cost-effectiveness in high-performance sawing for serial cuts up to 300 mm in diameter. This new generation of machines was also intended to rival the performance of the large circular saws previously used in this dimensional range.
The aim was to exhibit the new innovation for the first time at EMO 2019 in Hanover, the world’s leading trade fair for metalworking, in order to pique the interest of target customers and thus promote sales.
Until then, in the final phase of machine development, it was still necessary to realize the vibration-free use of the band saw blades to also enable rapid cutting of case-hardened and tempering steels as well as high-alloy structural steels with a diameter of up to 300 mm. The band saw blades previously purchased on the market were extremely susceptible to vibration. Under these conditions, in addition to a reduced lifetime of the band saw blades, it was also not possible to meet the usual required noise emissions.
The solution
WIKUS CARBIDE BAND SAW BLADES FOR HIGHEST CUTTING RATE
For the latest generation of machines in the KARMETAL portfolio – the ULTRA 300×300 – high-quality and high-performance carbide band saw blades were required. WIKUS FUTURA®, FUTURA® PREMIUM, and ARION® FG were the only products that met the requirements for processing performance, noise emission and lifetime.
Both FUTURA® PREMIUM and ARION® FG, with their special hard material- as well as the additional back edge coating, are used for serial cuts with the highest cutting rates in continuous operation and show a high reliability – even in automated production.
WIKUS thin-cutting technology for highest cutting speeds
In the performance test, the special WIKUS thin-cutting technology of the ARION® FG also enabled more saw cuts in the same time. Thanks to the reduction of the kerf, it also allowed sustainable handling of the cut materials. Thanks to their unique properties, these band saw blades were thus ideally suited for large-scale production and mass cutting processes in high-performance sawing applications and met KARMETAL’s technological requirements.
Because of the approx. 31% smaller kerf width of the ARION® FG (thin-cutting technology) and the cutting speed achievable by the ULTRA 300×300, a processing performance of up to 590 cm²/min was achieved during a performance test at KARMETAL. This performance was achieved on the material CK45/DIN No. 1.1191 with a diameter of 250 mm. Furthermore, ARION® FG allowed ULTRA 300x300 exceed the cutting speed of circular sawing machines and reducing the cutting kerf up to 60% with great productivity.
WIKUS supporting service



Any more questions?
The experts of our Technical Competence Center are happy to help you answer further technical questions connected to band selection and use.